Industrial designer Megan Valanidas uses bacteria-centered design to formulate bioplastics that decompose naturally.
Pivoting to Fight the Pandemic
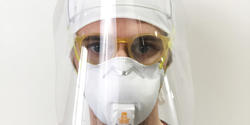
As COVID-19 patients overwhelm US hospitals from NYC to New Orleans to Seattle, medical personnel are risking their lives to provide quality care. In the absence of sufficient supplies of personal protection equipment (PPE) such as gloves and masks, their work is made that much more stressful.
A recent report in the Washington Postindicates that the federal government’s response to their desperate requests for emergency medical supplies and equipment has been slow and inconsistent from state to state.
At RISD students and faculty are conferring virtually about creative ways to meet worldwide demand, and Auxiliary Services recently donated N95 masks and safety goggles to the Rhode Island Department of Health.
Many RISD alumni who have carved out professional niches as creative entrepreneurs are pivoting to join the effort, rejiggering their studios and other fabrication sites to produce fabric masks or plastic face shields rather than apparel or home goods, for example.
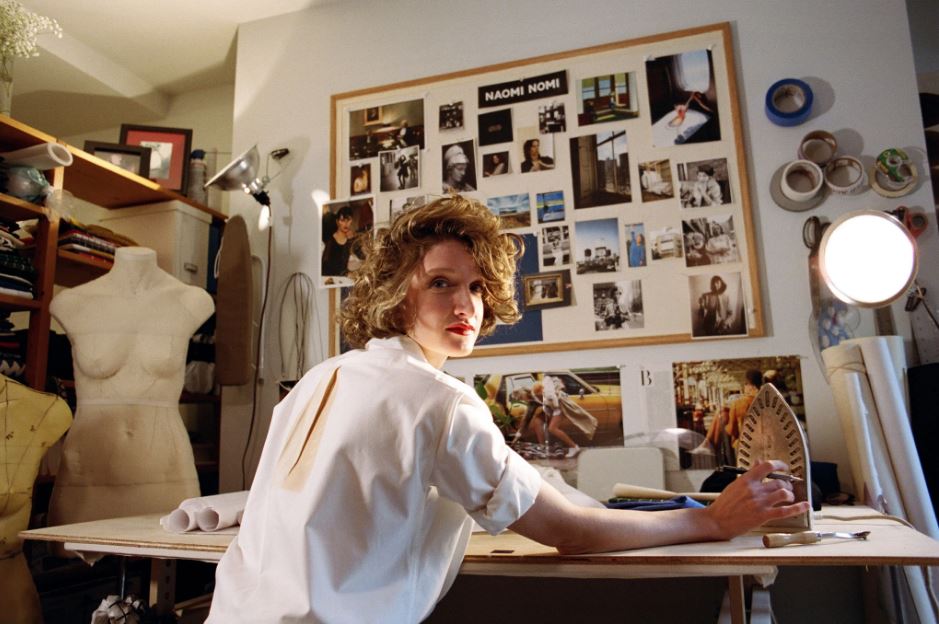
In Brooklyn designer Naomi Mishkin 11 GL, who launched the made-to-order line for working women NAOMI NOMI in 2018, is collaborating with her manufacturing partners to help local hospitals access more of the PPE they need. Given the lockdowns needed during the pandemic, “our production is completely on hold,” she says, “so we had to pivot. We had no choice.”
Mishkin is taking a two-pronged approach: sourcing materials to create hospital-grade masks at her facilities in Brooklyn and in Manhattan’s Garment District, and teaching fellow makers how to sew their own masks via Instagram workshops.
More than 25,000 people watched her recent New York Magazine Instagram takeover tutorial. “Making things helps people process,” notes the endlessly energetic entrepreneur.
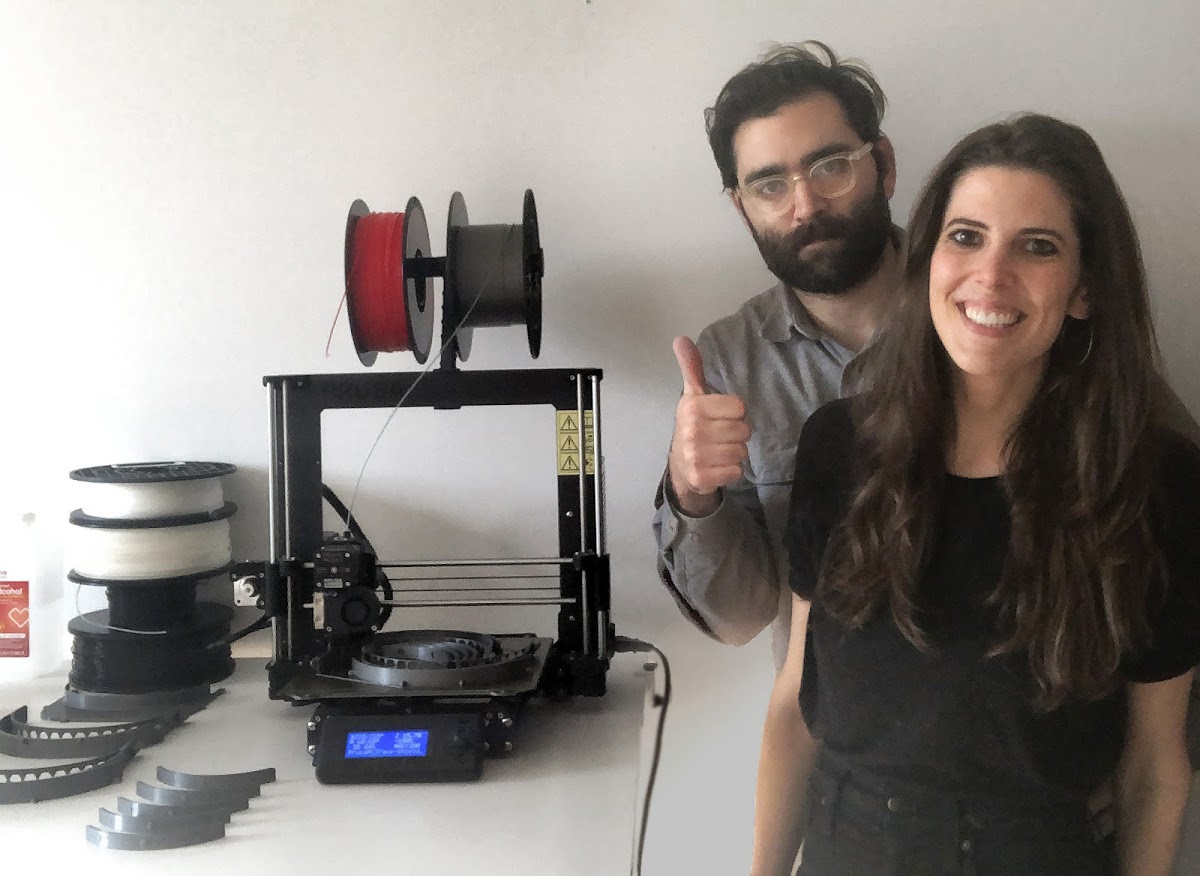
Also in Brooklyn, George Coffin 12 FD and Jillian Wiedenmayer BArch 12—coprincipals of the design consultancy Studio Den Den—are focusing on building community, raising funds via GoFundMe and producing hundreds of reusable, 3D-printed face shields for NYC health care providers.
“We quickly saw how dire the situation was,” says Wiedenmayer, “and it was glaringly obvious that we had the skills and the passion” to meet the need.
“Show me the tools and materials available, present a problem, and I won’t sleep until I’ve figured something out.”
“We vetted these products for function, comfort and ease of production,” the duo notes. “So far the prototypes are quite durable, offer flexible comfort, don’t fog up much and fit well over goggles and masks.”
Using the iterative process they honed as RISD students, Coffin and Wiedenmayer are attempting to improve their designs with every batch, beginning by sending multiple prototypes to partner hospitals and asking for feedback.
“We recently switched to a different open-source design by the Swedish 3D printing company 3DVerkstan,” they say, “which is simpler, prints faster and removes the elastic band from the equation.”
In terms of division of labor, Coffin is handling design, prototyping and printing, while Wiedenmayer is coordinating with hospitals and working with other designers to bring them up to speed. “We meet in the middle with assembly and—of course—critique,” she adds.
The design duo credits RISD with helping them develop problem-solving skills and the confidence it takes to step out of their comfort zones in a crisis situation. “Put me in a room, show me the tools and materials available, present a problem, and I won’t sleep until I’ve figured something out,” says Coffin. “That’s RISD in a nutshell.”
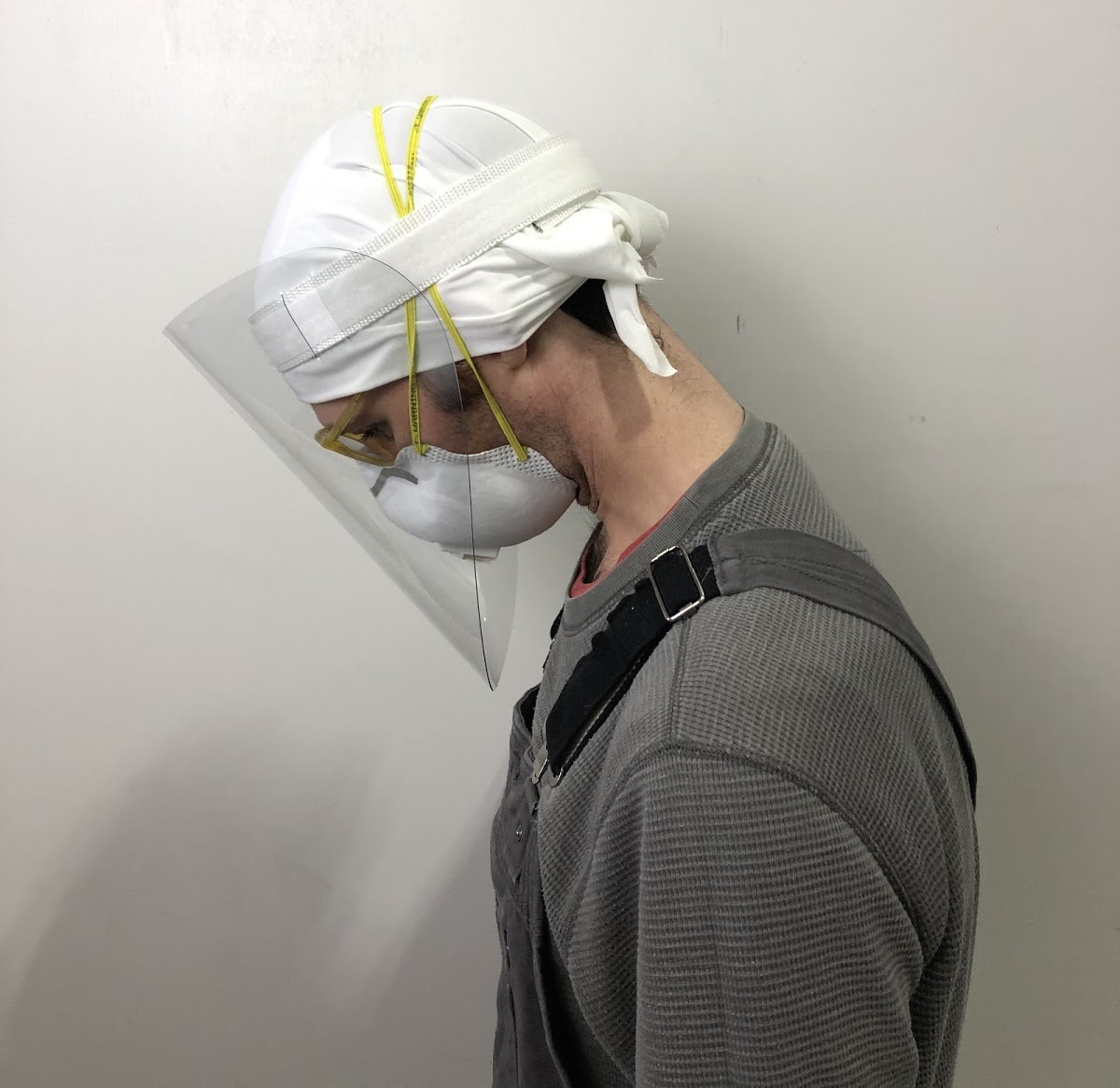
Coffin and Wiedenmayer are also talking with other RISD alums, including Mishkin, Rachel Paupeck MArch 12—principal of the interdisciplinary firm Montgomery—and industrial designer Josh Linder-Haber 12 ID, all of whom have manufacturing experience, partners and equipment they’re eager to share—and making those resources available on their website.
“It’s really important for people to connect and add what they can to the conversation,” says Mishkin, “rather than reinvent every wheel.”
“We’re distributing shields and masks directly to health care providers, postal workers... and other essential workers....”
Meanwhile on the other side of the world, apparel designers Aiala Rickard 17 AP and Isabel Sicat BRDD 16 IL of the Philippines-based label Toqa have temporarily set aside fashion to produce sustainably sourced, washable face masks. In Texas, jewelry artist Melissa Borrell MFA 05 JM is using her design, fabrication, project management and creative problem-solving skills in conjunction with the nonprofit collaborative Masks for Docs. And in Florida, tropical knitwear designer Karelle Levy 97 TX (KREL) is making tubular masks out of cotton blends that are machine washable and dryer friendly.
In Providence, textiles artist Jungil Hong 99 CR/MFA 15 TX is collaborating with designer Matt Muller 14 FD and his team at Pneuhaus, a maker of large-scale inflatables, on their own PPE supply chain while also organizing a large-scale purchase of surgical masks from China.
“Complex loopholes make it hard for hospitals to do this critical purchasing,” they explain, “so we’re distributing shields and masks directly to health care providers, postal workers, housing and social services advocates and other essential workers across many fields in Rhode Island, Massachusetts, New York and Maine.”
Hong’s and Muller’s approach to design and production is driven by available resources and the need for inexpensive, reusable face shields that can be easily sanitized on site.
“We got 30 of these clear vinyl prototypes into the hands of local doctors, and they love the fact that they can lay them flat and wipe them clean,” says Muller. “And we can make them for $2–3 per unit versus $8–10.”
“We can sustain our business and provide a product that’s a quarter the price of what’s out there because our design is so much simpler.”
The Velcro strap, Muller explains, can easily be removed and disinfected in a bucket of bleach solution. The Pneuhaus team is also making incremental improvements with each iteration.
“We have the capacity to make between 1,500 and 3,000 shields per day once we get going,” says Muller, “which means we can sustain our business and provide a product that’s a quarter the price of what’s out there because our design is so much simpler.” His team has also launched a GoFundMe page to get production rolling.
Muller says that the all-consuming effort is actually helping with team morale, noting that “it feels good to do something.” And the Den Den duo concurs, encouraging other alums as well as current RISD students to “get involved and do everything they can to help.” After all, they point out, “Netflix will still be there when this is all over.”
—Simone Solondz
Tune into @risd1877 on Tuesday, April 7, for a mask-making tutorial with Naomi Mishkin.
March 31, 2020