Longtime Professor Anais Missakian 84 TX is honored to accept her new appointment as RISD’s first Pevaroff-Cohn Family Endowed Chair in Textiles.
Bold Breakthroughs in 3D Weaving
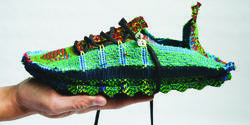
Associate Professor of Textiles Brooks Hagan MFA 02 TX and Steve Marschner, a computer science professor at Cornell, continue to push the bounds of digital fabrication. From creating the virtual loom Weft to a “library of [3D woven] tendencies,” their Virtual Textiles Research Group (VTRG) is actively expanding knowledge in the field.
Consider Weavecraft, open-source design tool developed by the VTRG (with hard-coding and UI implementation by computer scientists from Cornell and Stanford). Benefitting from the specialized resources of the Rhode Island-based company TEAM, the research group has figured out how to weave an athletic shoe on a loom—a feat Hagan sees as “a real triumph.” Additionally, the group's research on fiber and yarn simulation has also led to a multiyear partnership with the sporting goods brand Under Armour.
Having presented their work at the most recent SIGGRAPH interactive technologies conference, Hagan and recent grads Claire Harvey 18 TX and Emily Holtzman 18 TX shared their insights about the incredible potential for 3D weaving.
What are you aiming to achieve with Weavecraft and other VTRG research?
Hagan: Where other 3D fabricating zones have benefitted from advanced CAD systems and visualization, textiles has lagged. It’s a complicated problem because we have to consider not only how fabric looks but also how it behaves and how yarns are assembled through really complex—sometimes robotic—manufacturing techniques.
There’s an endless amount of work to be done to improve how we interact with textiles in a computer environment. But if Weavecraft can provide a simplified way of approaching this work bit by bit, [it will be like] 3D printing, where you can design an object and execute it in soft materials—and predict its soft behavior.
“In the hands of really creative people this technology can take textiles in directions we haven’t even thought about.”
Is the software mostly geared toward manufacturing and industrial production or does it have implications for fine art or other custom work?
Holtzman: I think that a visualization and design tool like this—one that can make the really complex and dense process of 3D weaving easier—can help open the doors to wildly disruptive innovation. And [personally], by continuing research towards [creating] a strong visualization tool, I will be able to design more quickly and productively.
Hagan: The benefits of improving vision in the textiles space are numerous. Not only would it cut down on tremendous amounts of waste but also on the time it takes to iterate. With better tools we can zero in on what’s promising tremendously faster. And from there we can make better things.
In the hands of really creative people this technology can take textiles in directions we haven’t even thought about. And engineers and others can put it toward designing buildings, medical [tools and devices]—you name it.
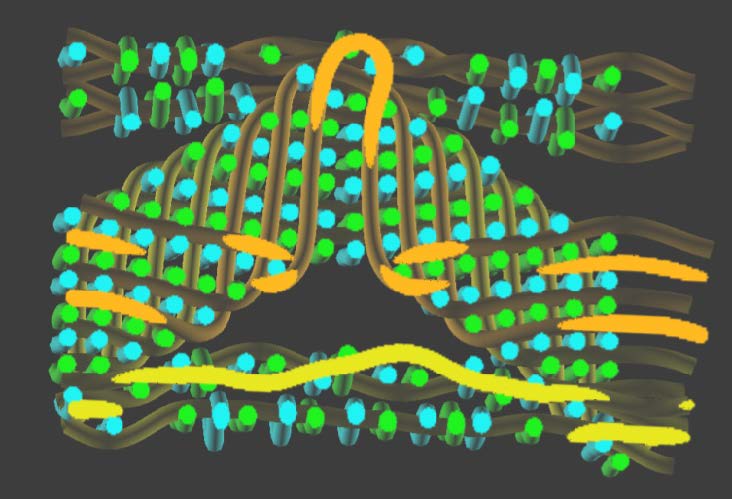
What went into the design and execution of making the shoe at TEAM?
Holtzman: Trial and error! We thought through what parts of the process need to be visualized to make future iterations easier and then how to communicate design challenges to the computer scientists at Cornell that they could use to inform the software. By vertically integrating all the different processes that go into shoe manufacturing, I think we made a really disruptive product.
“It’s not very often that the textile is the [entire] thing.... There’s a poetry in that.”
Hagan: Where we are now with the technology, it took us nine months to get to where we could even comprehend creating a [3D-woven] shoe—to understand all the issues and layers and how they might connect. But once you can establish the basic idea of “shoe” as your starting point, then what you make can be so much more sophisticated, customized or varied.
In textiles we create so much that is meant for application, whether it’s upholstery or apparel or—on the technology side—integrated fibers. But it’s not very often that the textile is the thing. That’s a really compelling piece of this. We were able to weave an entire shoe on looms. There’s a poetry in that.
“A visualization and design tool like [Weavecraft] can help open the doors to wildly disruptive innovation.”
What is the collaboration between VTRG’s designers and computer scientists like?
Harvey: Working alongside computer scientists [like Marschner and Rundong Wu, a PhD candidate at Cornell] has made jumping into 3D weaving after studying 2D fabrics a really magical experience.
On this project, whenever we hit roadblocks or realized that we wanted to try something new, we were able to have in-depth conversations with really smart computer scientists about some of the most tedious parts of weave drafting—things that normally most people aren’t interested in having with us.
Hagan: At a higher level, in textiles we’re dealing with legacy systems that have gone literally unchanged for hundreds of years. Given how sophisticated digital rendering is in architecture, interior architecture, car design and so on, why aren’t we getting more information in textiles? And what will we be able to do with better information? Everybody on the team is motivated to work toward that.
“Working alongside computer scientists has made jumping into 3D weaving after studying 2D fabrics a really magical experience.”
How does this project impact your own practices and how textiles will be taught in the future?
Harvey: This project has opened my eyes to the world of academic collaboration and research. [As textiles designers], we are not alone in this world or limited to the skillsets we have. It’s possible to join forces with other people and create new and exciting things that can’t emerge from a single person’s creativity or volition.
It’s really exciting to see weaving capture the imagination of people with different expertise. I want to keep working and collaborating in this way for as long as possible!
Hagan: As [textile manufacturing] equipment becomes more robotic and the standard binary languages we’re accustomed to working in—on/off, up/down—become more grayscale, we will need better tools to make these shadings and new possibilities part of the design process.
Weavecraft is still very technical, so we will need a better on-ramp for bringing programs like it into the studio. But what we’ve already been able to do suggests that there are all sorts of architectures that we can create in this space. And that is super exciting.
—interview by Robert Albanese
August 5, 2019